Saving Time, Labor, and Money with Pneumatic Batch Blending
With a pneumatic blender, you can mix batches of dry bulk materials in the conical hopper of a storage vessel or dense phase pneumatic conveying transporter rather than in a mechanical mixer, yielding real savings in time, labor, and capital equipment costs. After explaining how the pneumatic blender works, this article describes its applications and benefits and details how testing can help you select the blender for your application.
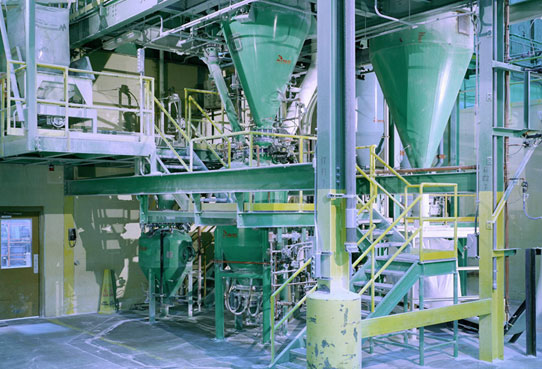
Pneumatic blending in a bin or silo — that is, aerating materials with compressed air to mix them within the vessel — has been used for decades as a way to homogenize large production runs of a single material. For instance, cement producers inject compressed air through the floor of a flat-bottom silo to aerate various sections of the stored cement in sequence, changing the cement’s bulk density to ensure that the discharged cement represents a wide range of the entire production run. Plastic pellet producers often continuously recirculate pellets from a silo’s discharge area to the silo’s top to mix pellets from yesterday’s production run with today’s pellets.
You can use the same pneumatic aeration technique to actively blend an entire batch in one mixing cycle by integrating a pneumatic blender (also called an air blender) into your material handling system. Because the blender provides mixing in your vessel or dense phase pneumatic conveying transporter, it eliminates the need for a separate mechanical mixer. The blender also minimizes material handling, reducing labor and equipment costs.
How the pneumatic blender works
Unlike a mechanical batch mixer, in which ingredients are measured and loaded into the mixer, mixed by a mechanical agitator or other mechanical means, and discharged from the mixer to a material handling system, the pneumatic blender is generally integrated with the material handling system.
The pneumatic blender is mounted at the bottom of the conical discharge hopper of a storage vessel, as shown in Figure 1, or dense phase pneumatic conveying transporter. The blender consists of a conical housing called a blending cone (or cone casting) that’s mounted with several aeration valve assemblies. Each valve assembly includes an air cylinder and valve air seal and is connected to a compressed-air supply. The supply pressure to the valve assemblies is controlled by a regulator on the compressed-air supply’s manifold. The valve assemblies are installed around the blending cone at different angles so they can inject compressed air upward into various areas in the hopper. An outlet valve, most often a pneumatically operated butterfly valve that’s linked to the blender controls, is at the blending cone’s bottom.
In operation, ingredients for the batch are fed one at a time by gravity or pneumatically into the vessel, forming layers. When the controls activate the blender, the aeration valve assemblies inject gentle pulses of compressed air through the blending cone into the center of the vessel’s hopper section. The injected air expands in volume, aerating the material in the hopper bottom and gently lifting it. This aerated material now has a lighter bulk density than the material above it, causing the lighter material to migrate upward while gravity draws the heavier material downward (Figure 1). The interaction of the upward- and downward-flowing materials mixes the entire batch. The blending action is controlled by the air pulses’ frequency, duration, and pressure. Since these pulse variables depend on the characteristics of each batch ingredient and the batch size, they must be determined by testing in the blender supplier’s lab (discussed later in this article).

Once blending is complete, the outlet valve opens and the batch discharges by gravity into the downstream handling system or process. When the blender is used on a storage vessel, the outlet valve is often connected to a dense phase conveying system because the system’s low transport velocity will convey the blended batch without segregating it.
Controls. Depending on the application, the blender can be controlled from a control panel at the blender or a remotely located PLC. Either can be preprogrammed with pulse settings for individual batches.
Optional aeration gas. The aeration valve assemblies can also inject an inert gas, such as nitrogen, rather than air in blending applications with explosible materials, with materials that are sensitive to excessive amounts of oxygen, or in which the gas must contain no moisture.
The pneumatic blender is best suited to materials with an average particle size under 1⁄8 inch because these materials aerate easily.
Suitable applications
The pneumatic blender can be installed in the conical hopper of either a new or existing vessel. However, for a retro-fit application, the existing vessel must have a hopper cone angle 60 degrees or steeper and must be structurally capable of withstanding the blending cone’s weight and the pressure loading applied during blending.
The pneumatic blender’s gentle mixing action makes it especially suitable for blending batches containing friable materials, such as glass bubbles and spray-dried milk, whey, and clay powders. The blender is also well-suited to mixing abrasive materials; the unit’s gentle action and few moving parts in contact with the material (including only the valve air seals in the aeration valve assemblies and the outlet valve) minimize the material’s abrasive effects.
However, the blender’s gentle action also typically makes the unit unsuitable for materials that require shear to become fully mixed. Some cohesive materials, such as titanium dioxide or iron oxide, aren’t candidates for pneumatic blending because they don’t aerate easily despite their fine particle size; the blender will simply blow holes through the material unless it’s mixed with another material that promotes aeration. To determine whether the pneumatic blender can mix your difficult-to-aerate material, you’ll need to have the material tested in the supplier’s lab.
Pneumatic blending benefits
Minimizing needed equipment, floor space, material handling, and costs. One of the greatest pneumatic blender benefits is that it uses a storage vessel or transporter as the blending vessel, so it requires no separate piece of equipment for mixing and no floor space for that equipment, as a mechanical batch mixer would. The pneumatic blender also allows you to mix a large batch in the storage vessel or transporter, saving the time required to transfer the batch into and out of a separate mixer. This also reduces the amount of handling the batch requires, conserving labor and reducing your capital equipment costs, especially when the blender is used in a transporter.
Blending gently and rapidly. In addition to being well-suited to handling friable and abrasive materials, the pneumatic blender’s gentle mixing action minimizes material attrition and maintains the batch’s overall integrity without segregating ingredients. For easily aerated ingredients, the pneumatic blender’s cycle time is typically much shorter than that of a comparable mechanical mixer.
Flexibility. Mixing with the pneumatic blender can be controlled to meet your batch blending requirements by adjusting the frequency, duration, and pressure of the air pulses. Your operator can manually change these settings on the controls or, when batches of different ingredients will be blended in the same vessel, can simply select the desired batch settings from those preprogrammed into the controls. The blender can also be adjusted for your vessel size. If your blending application requires liquid addition, the blending cone can be fitted with atomizers for spraying a small amount of liquid into the batch.
Minimizing maintenance and cleaning. The pneumatic blender provides a long service life with little maintenance because it has few moving parts in contact with the material, unlike a mechanical mixer with agitators. The pneumatic blender’s gentle mixing action also minimizes blender wear.
The blending cone and aeration valve assemblies are accessible from outside the vessel, making service easy and fast. As a result, the pneumatic blender costs less to maintain than a mechanical mixer in the same application.
Another benefit of having few moving parts in contact with the material is that, in most applications, the pneumatic blender requires little or no cleaning. In applications that require complete cleanout between batches, a “cleanout batch” of scrap or low-cost material (such as sand, limestone, or fly ash) can be run through the blender and discarded before the new batch is blended. For instance, when the blending vessel in a cement mix plant switches from running a dark cement mix to a light mix, the plant can run a cleanout batch of cement that has no colorant to remove the dark pigment from the vessel. For applications that require more thorough cleaning, the blending vessel can be equipped with a clean-in-place system that uses an appropriate cleaning liquid to wash down the interior walls.
Testing to select the right blender
The pneumatic blender supplier will ask for detailed information about your blending application to help you select a pneumatic blender. This information will also help the supplier decide what kind of testing is required to select the right blender size, features, and air-pulse settings for your application.
Your application details. The supplier will typically ask you to provide this information:
- Characteristics of each batch ingredient (including bulk density, particle size distribution, temperature, moisture content, hygroscopicity, explosivity, toxicity, corrosive-ness, and others).
- Your desired batch size and the proportions of each ingredient per batch (such as 25 percent ingredient A, 40 per-cent ingredient B, and 35 percent ingredient C).
- Any variations in the ingredients or their proportions in your current or future batch formulations.
- Details about the process or handling systems upstream and downstream from the blender.
- Your available blending time per batch.
- The available physical space in your plant (for new installations).
- Special electrical classification requirements.
- Dust collection requirements.
- What aeration gas (such as compressed air or nitrogen) you’ll use and how it will be supplied to the blender.
Testing. The blender supplier will typically run tests with your ingredients in a full-scale pneumatic blender. At minimum, you’ll need to ship ingredients for a 10-cubic-foot batch to the supplier, depending on the lab blender’s size and your batch size. The closer the quantity of material you ship to your actual batch size, the more closely the tests can simulate your application requirements and the more confidence you can have in the results.
During the tests, the lab staff will determine how to adjust the air-pulse frequency, duration, and pressure to achieve your desired blend quality with your ingredients and batch size.
Before the pneumatic blending tests begin, the lab staff will usually run their own tests of your ingredient characteristics, such as poured, packed, and aerated bulk density, particle size distribution, moisture content, and angle of re-pose. The results will help the staff design the blending tests for your ingredients.
For best results, you should plan to witness the blending tests in person. During the tests, the lab staff will determine how to adjust the air-pulse frequency, duration, and pressure to achieve your desired blend quality with your ingredients and batch size.
Once the tests are completed, the lab staff can also advise you about other blender design and operation factors to consider for your application, including the following:
- Blending cone size: The combination of your batch size and the time available for mixing will determine the blending cone’s size. For instance, if your batch size is large and the time available for mixing is short, a larger blending cone with more aeration valve assemblies is required; if your batch is large but more time is available for mixing, you can use a smaller blending cone with fewer valve assemblies.
- Venting: Because the pneumatic blender uses large pulses of compressed air to mix materials, the air must be vented from the blending vessel. The best way to do this is to vent the air to a bin vent that’s located at the vessel’s top and adequately sized to handle this large air volume. The bin vent will filter fines from the vented air and return them to the vessel instead of passing them to the plant’s central dust collection system, thus maintaining the batch quality.
- Discharging: To prevent your batch from segregating during discharge, especially when the blending vessel is very large, the pneumatic blender’s outlet valve must be designed to close on the material flow stream at any time during the discharge process. Because there’s a slight positive pressure in the area near the blending cone during the air pulses, the outlet valve must also be able to close tightly without leaking air. Then, when the valve is closed, the blender can inject additional air pulses into the material to reblend the partially discharged batch, ensuring blend homogeneity during a long discharge process. While the most common outlet valve is a butterfly valve, some applications require a rotary valve, such as when the batch must be metered from the blender into a process.
- Preventing material from entering the compressed-air source: The blender must be designed to ensure that no particles from your batch can enter the compressed-air source. If air pulses occur when the compressed-air supply manifold is at a lower pressure than the blending vessel pressure, particles from the batch can migrate from the higher-pressure vessel into the lower-pressure compressed-air supply. The best safeguard is to equip the blender with a pressure switch or transducer that monitors the pressure at the manifold and prevents the aeration valve assemblies from pulsing if this pressure is lower than the vessel pressure. As long as the manifold is at a high pressure than the blending vessel, particles can’t migrate into the compressed-air supply, even if one of the valve assemblies leaks.
Key Takeaways
Pneumatic blending in a bin or silo — that is, aerating materials with compressed air to mix them within the vessel — has been used for decades as a way to homogenize large production runs of a single material.
- Pneumatic blending is one of the quickest, cleanest, and most efficient methods of achieving homogeneous batches of powdered, granular, fragile, and/or abrasive materials.
- Pneumatic blenders are typically integrated within the material handling system saving time, money, and floor space.
- Pneumatic blenders come in many sizes with customizable features to ensure batch ingredients, size, and time meet your specific process requirements.
How can we help?
Maybe you need a new system, an upgrade to an existing system, or a retrofit. Regardless of size, industry, or material, we are here to help you get your project and product moving.
Get in touch