BATTERY PRODUCTION PNEUMATIC BLENDER
For the best in dry material blending technology for battery production facilities, Nol-Tec Systems is the clear choice. Our industry-leading blending solutions offer reliable, efficient performance that will keep your production facility running smoothly.
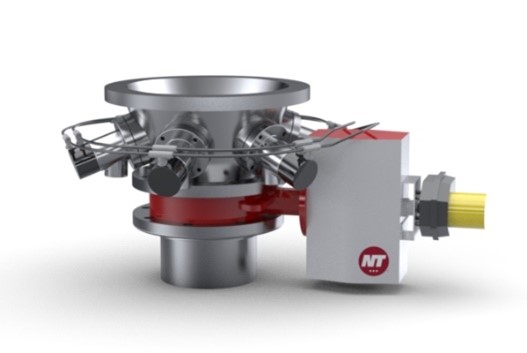
Nol-Tec Model: M244 or M277
If you have a battery production facility that requires a blending of dry materials, then you should look no further than Nol-Tec Systems industry leading blending technology, our Model M244 or M277. The technology has been supplied to battery process plants around the world since the early 2000s, and successfully pneumatically blends common battery materials, such as metal hydroxides, lithium hydroxides and similar difficult to handle materials – Simply put, it is an industry proven workhorse with many advantages as explained below.
Function: it is a unique pneumatic blending cone, installed in the discharge of both bins and silos. This cone utilizes “pulses” of compressed air, or other gas, to effectively mix powdered or granular bulk solid materials into a homogeneous mixture.
Blending technology, loaded with unique features: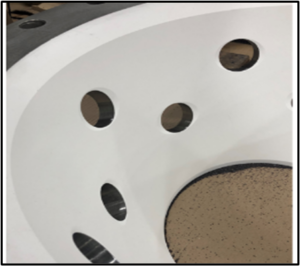
Reduction in metal contamination – short circuits between electrodes and poor battery performance is often a result of contamination in manufacturing. We developed ceramic coating specifications to ensure that no contamination from the actual blender equipment is allowed to contaminate the battery process.
Back-feeding/elimination of cross contamination – the blend cone is under positive pressure – this design almost completely eliminates the risk of material “back-feed” from the blend bin into the air supply manifold, (an issue which many other pneumatic blenders without this design suffer from frequently). This design feature also prevents any material from staying in the blender after batch discharge, eliminating the possibility of material cross contamination between batches, resulting in a more hygienic process.
Limited discharge segregation – materials tend to segregate during discharge – to overcome this our outlet valve can be opened or closed at any time during discharge, and therefore gives the ability to close the valve, pulse the blender a few times and therefore
minimize or eliminate the discharge segregation issue.
Ease of maintenance – if a blending piston fails, it can be removed and replaced without dismantling the entire cone assembly or taking it out of the blending bin.
Gentle handling – this pneumatic blender is uniquely suited to handle abrasive products and those that require a gentle blending action. Other mechanical and pneumatic blenders are not as capable in these conditions.
Batch size options – our Model M244, designed with 6 pistons is sized to blend up to 400-500ft3 (11-14m3) and for larger batches, our Model M277, with 12 pistons, is designed to attach directly to the bottom of a silo and can handle batch sizes of approximately 3,000ft3 (85m3) / 4-5,000ft3 silos.
Low pressure – M277 and M244 design requires much lower pressures to blend materials properly in comparison to other pneumatic blenders. The blend pressure typically ranges from 20 to 70 PSI, but this may vary depending on the characteristics of the material, batch
size, and the customer’s blending process.
Blends materials with varying bulk density and particle sizes – the blender cone utilizes a combination of material fluidization and dynamic material movement to achieve effective blending, unlike other pneumatic blenders which only employ fluidization. These features also ensure a lower batch time than other mechanical and pneumatic blenders.
To find out more about how we can help, check us out on our website www.nol-tec.com, use the contact form Contact Us | Nol-Tec or call us at +1 (651) 780-8600.
Key Takeaways
This Pneumatic Blender utilizes “pulses” of compressed air, or other gas, to effectively mix powdered or granular bulk solid materials into a homogeneous mixture.
- Reduction in metal contamination
- Back-feeding/elimination of cross contamination
- Ease of maintenance
- Gentle handling
How can we help?
Maybe you need a new system, an upgrade to an existing system, or a retrofit. Regardless of size, industry, or material, we are here to help you get your project and product moving.
Get in touch